Entwicklung eines lasttragenden und crashrelevanten Metall-GFK-Karosserieteils
Abgeschlossenes Projekt
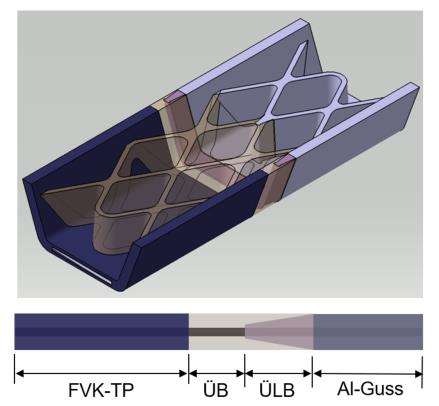
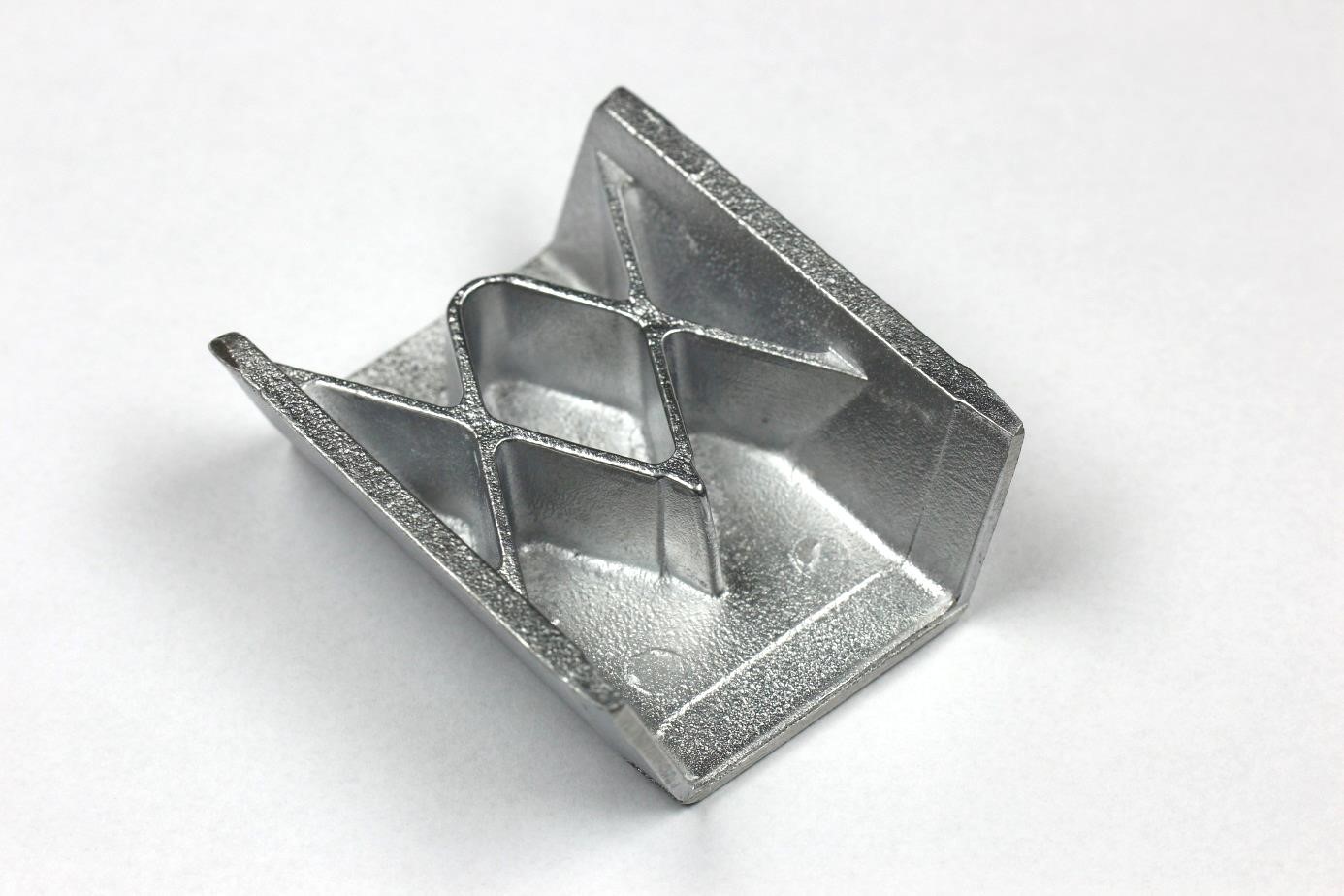
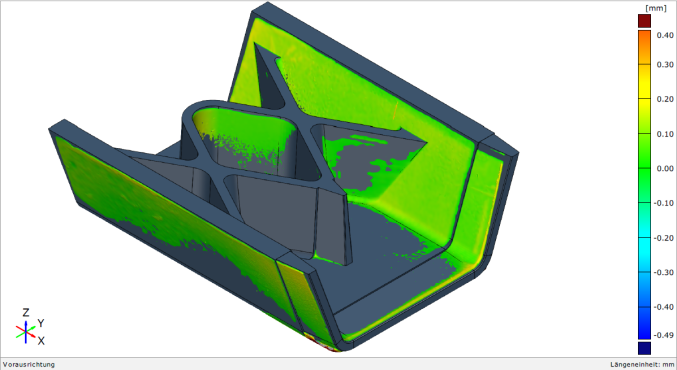
Im Projekt »EnTraHyb« entwickelt das Fraunhofer-Projektzentrum Wolfsburg in Kooperation mit der Technischen Universität Braunschweig eine tragende, crashrelevante Metall-FVK-Baugruppe für PKWs. Dabei werden Glasfaserhalbzeuge als Übergangsstruktur zwischen einem Aluminium-Gussknoten und einem im Spritzguss sowie Heißpressverfahren hergestellten thermoplastischen Faserverbundwerkstoff zu einer kraftflussgerechten hybriden Demonstratorstruktur verarbeitet.
Im automobilen Karosseriebau sind vor allem metallische Bauteile, wie Stahlblechvarianten, Aluminiumstrukturen und Aluminiumguss, von hoher Relevanz. Der Multi-Material-Mix mit konventionellen Werkstoffen und Faserverbundwerkstoffen hingegen ermöglicht ein unübertroffen hohes Leichtbaupotenzial. Um diesen vollständig ausschöpfen zu können, sind neue Prozess-Technologien zur Herstellung von Hybridbauteilen erforderlich. Im Projekt »EnTraHyb« liegt das wesentliche Ziel in der Herstellung eines neuartigen hybriden Demonstratorbauteils. Die Untersuchung der Wechselwirkungen verschiedener Prozesse und Technologien zu dessen Herstellung wurde anhand des Demonstrators in den Vordergrund gerückt.
Zur Herstellung des Demonstrators wurden Glasfaserhalbzeuge in einen Gussknoten integriert und im Niederdruck-Gießprozess partiell von Aluminiumschmelze umgossen. Dazu wurden zunächst Kleinproben in einem Versuchswerkzeug hergestellt und getestet. Darauf aufbauend wurde ein Werkzeug zur Herstellung der Gussknoten in zwei unterschiedlichen Ausprägungen entwickelt und gefertigt. Durch einen Wechseleinsatz war es so möglich, Bauteile mit Gussrippen und ohne Gussrippen abzubilden sowie Fasern direkt im Gießprozess mit in das Aluminium einzubringen.
In einem Folgeprozessschritt wurden die von Aluminium abgeschirmten, nichtinfiltrierten Faserhalbzeuge mit thermoplastischen Halbzeugen im Heißpressverfahren umgeformt und zu einem Faserverbundwerkstoff konsolidiert. Besonderes Augenmerk lag dabei einerseits auf der endkonturnahen Formgebung direkt im Pressprozess und andererseits auf der Umsetzung des Pressprozesses mit hybriden Strukturen.
Die Übergangszone zwischen dem Aluminiumguss und dem Faserverbundwerkstoff wurde in einem dritten Prozessschritt im Spritzgießverfahren hergestellt und gleichzeitig eine Rippenstruktur auf das Hybridbauteil aufgebracht. Zur Verbesserung der Haftung zwischen Aluminiumgussoberfläche und dem thermoplastischen Kunststoff wurden verschiedenen Oberflächenbehandlungen getestet. So wurden das Aufbringen eines Haftvermittlers, das chemische Ätzen oder auch die Oberflächenstrukturierung mittels Laser untersucht. Durch den Einsatz der Laserstrukturierung konnte die Verbundfestigkeit zwischen Aluminium und Kunststoff bedeutend verbessert werden. Die nichtinfiltrierten Faserhalbzeuge im Übergangsbereich wurden mit Kunststoff infiltriert und das Infiltrationsverhalten in Abhängigkeit der Faserlagen im Spritzguss untersucht.
Um die seriennahe Umsetzbarkeit zu erfüllen, erfolgte parallel die Untersuchung automatisierbarer Prozessabläufe. Begleitet wurde das Projekt von einer simulationsgestützten Bauteilauslegung und -optimierung, der Untersuchung des Versagensverhaltens sowie der mechanischen Werkstoffprüfung der Hybridstrukturen. Zur Abbildung des gesamten Lebenszyklus wurde die Rezyklierbarkeit der Hybridbauteile untersucht.