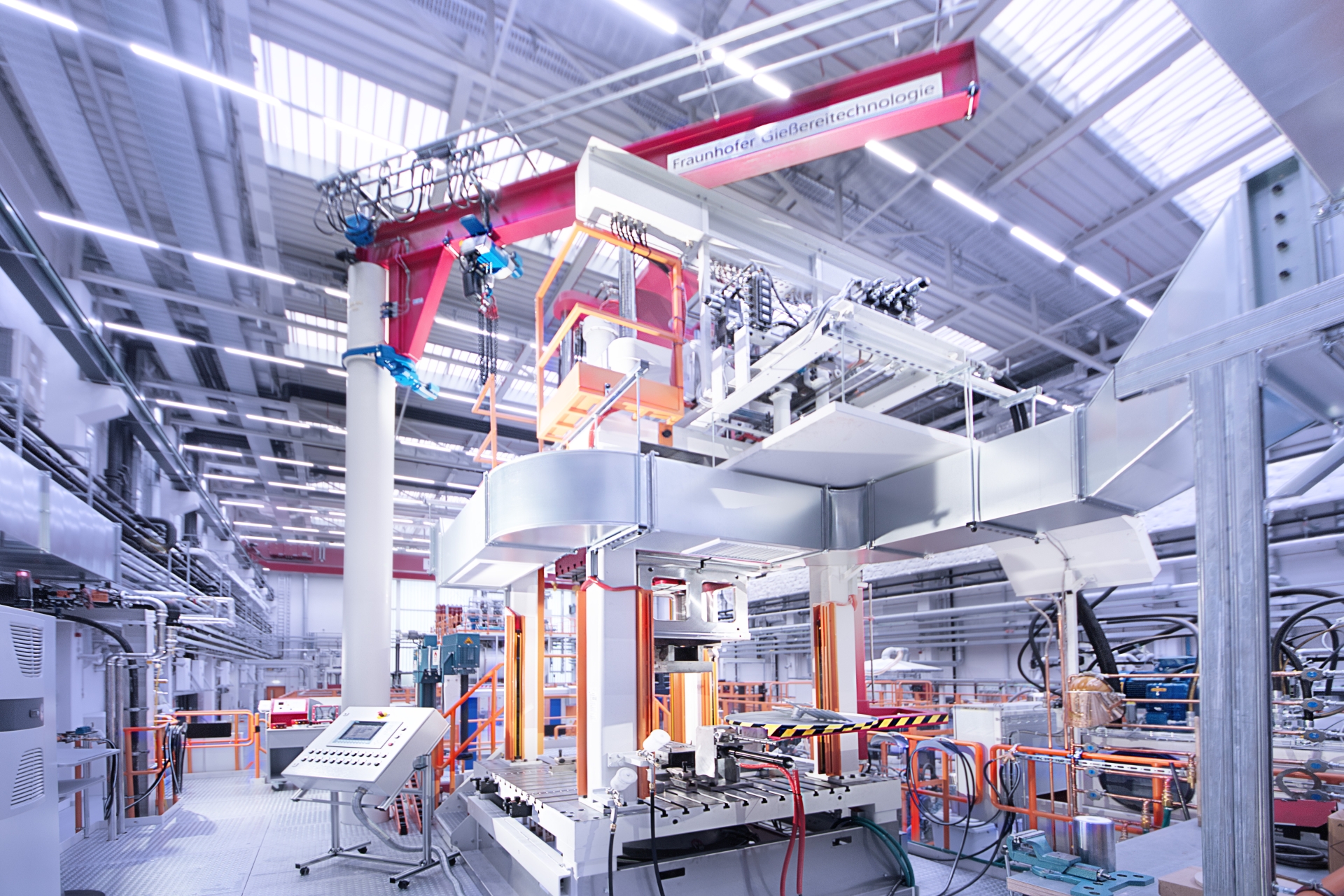
Die Niederdruckgießanlage mit hydraulisch betriebener Schließeinheit und ausfahrbarem Schmelz- und Warmhalteofen dient dem Vergießen von metallischen und nichtmetallischen Werkstoffen. Im Niederdruck-Gießverfahren können Bauteile mit höchsten Anforderungen an die Gussqualität, Gussteil-Komplexität, Werkstoffauswahl und werkstoffliche Eigenschaften hergestellt werden. Mit der Niederdruckgießanlage vom Fraunhofer-Projektzentrum Wolfsburg kann ein automatisierter, seriennaher Gießbetrieb dargestellt werden. Der induktive Shuttle-Ofen ermöglicht den Einsatz verschiedenster Gusswerkstoffe wie Aluminium, Magnesium, Stahl, Kupfer, Messing und Salz.
Durch hohe Stückzahlflexibilität ist die Herstellung von Prototypen ebenso möglich wie eine Serienfertigung. Eine Besonderheit stellt die Fertigung von hybriden Vergussbauteilen dar. Im sogenannten Hybridguss sind verschiedene Materialkombinationen aus Aluminium-FVK, Aluminium-Stahl, Aluminium-Aluminium oder Aluminium-Kunststoff denkbar. Ein weiterer Schwerpunkt liegt auf der Entwicklung neuer Produkte und Fertigungsmöglichkeiten für Elektroantriebe. Beispiele für diese Bauteile sind gegossene Spulen, Statorgehäuse oder infiltrierte Blechpakete.
Weitere Informationen zur Gießereitechnologie.